-
Currency:Localize your Content
You can set your preferred currency for this account.
Choose a Currency
Currency- CHOOSE YOUR CURRENCY
Update Currency
Changing Currency will cause your current cart to be deleted. Click OK to proceed.
To Keep your current cart, click CLOSE and then save your cart before changing currency.
-
Select Account1
Switching accounts will update the product catalog available to you. When switching accounts, your current cart will not move to the new account you select. Your current cart will be available if you log back into this account again.
Account# Account Name City Zip/Post Code My Account -
-
Products
- Complete Combustion Solutions
- Fuel & Air Delivery
- Burner Management Systems
- Burners & Heat Exchangers
- Complete Combustion Systems
- Software
- Control & Supervisory Systems
- Field Instruments
- Gas
- Marine
- Process Instruments
- Training
- Spare Parts
- Terminals
- Thermal Solutions
- Wireless
- Uncategorized
- Quality Control Systems
- Trainings
- Utilities
- View All Manual Valves & Filters
- Adjustable Orifice Valves (ALO/ALO-R)
- Manual Shutoff Valves
- Disk Type Check Valves
- A Style Synchro Valves
- Flow adjusting cocks GEHV, GEH, LEH
- Manual valves AKT
- Manual valves with thermal equipment trip AKT..TAS
- Shut off valves ZIVA
- Thermal equipment trips TAS
- Gas filters GFK
- View All Pressure Regulators
- Kromschroeder VAD-VAG-VAH-VAV pressure regulators with solenoid valve
- Safety shut-off valves JSAV
- Pressure regulators for gas GDJ
- Gas Pressure Regulators Maxon
- Pressure regulators for gas VGBF
- Pressure regulators for gas J78R, 60DJ
- Air/gas ratio controls GIK
- Relief valve VSBV
- Circulation pressure control and relief regulators VAR
- Variable air/gas ratio controls GIKH
- SmartLine Wireless Differential Pressure
- View All Shutoff Valves
- Kromschroeder VAS-VCS solenoid valves for gas
- Kromschroeder VAN magnetic relief valves
- High Pressure Electro-Mechanical Oil Shut-off Valves
- Series 8000 Air Actuated Valves for Liquid Service
- NI Series Hazardous Duty Valves
- Series 8000 Pneumatic Safety Shut-off Valves
- High Pressure Electro-Mechanical Gas Shut-off Valves
- Solenoid-operated butterfly valves for air MB 7/BVHM
- Solenoid valves for air VR
- Solenoid valves for gas VG
- Motorized valves for gas VK
- Solenoid valves for gas VGP
- View All Control Valves
- Discontinued - Honeywell SV2 combination valve
- SMARTLINK® CV Electronic Valves
- Micro Ratio Valves (M-P-O Style)
- SMARTLINK® MRV Electronic Ratio Valves
- Self-Cleaning Micro Oil Valves MOV
- Control valves RV, control valves with solenoid valve RVS
- B, F, G, & K Micro Cam Oil Valves MCOV
- Solenoid valves for gas VE, V4295
- VR400/VR800 Series
- VQ400/800 Series
- View All Pressure Switches & Gauges
- Honeywell C6097 pressure switches for gas
- Kromschroeder DL..A pressure switches for air
- Kromschroeder DG pressure switches for gas
- Kromschroeder DL..K pressure switches for air
- Kromschroeder DG..C pressure switches for gas
- Kromschroeder DL..E pressure switches for air
- Elektronic pressure gauge DMG
- Pressuretrol® Limit controllers L4079A, B, W
- Pressure gauges KFM, RFM
- Pressure Indicators PI
- PressureTrol® Pressure monitoring on/off controllers L404F, T, V
- PressureTrol® Pressure monitoring modulating controllers L91A, B
- CPS
- Pressure switches for gas DGM, DWR
- Vaporstat ® Controllers L408J
- View All Burner Control Units
- Kromschroeder BCU 400 burner control unit
- Honeywell 7800 SERIES burner control unit
- Kromschroeder IFD 258 burner control unit
- Kromschroeder IFD 244 burner control unit
- Automatic burner control units for continuous operation PFD 778
- Automatic burner control units for continuous operation IFD 450, 454
- Automatic burner control units IFS 110IM, 111IM
- Burner control unit BCU 370
- Relay module 7800 Series
- Burner control units BCU 560, BCU 565, BCU 580
- Automatic burner control units PFS 778, 748
- Burner control unit BCU 570
- Automatic burner control units PFU
- Automatic burner control units IFS 132B, 135B, 137B
- View All Flame Detectors
- Heat Block Seal
- Ignition Transformers Q652
- UV sensor for continuous operation UVC, UVD
- Flame detectors PFF
- Flame detector for continuous operation IFW 50
- UV sensors UVS
- Ultraviolet Flame Detector C7012A,C
- Flame detector IFW 15
- Ultraviolet Flame Detector C7027, C7035
- Ultraviolet Flame Detector C7927
- Ultraviolet Flame Detector C7915
- Ultraviolet Flame Detector C7076A,D
- Ultraviolet Flame Detector C7961E,F
- Ultraviolet Flame Detector C7061A,F
- View All Industrial Flame Monitoring (IFM)
- Gas Igniters GHE
- Viewing Heads S70X/S80X
- Model P532
- FASA Glass and Quartz Fiber Optics
- Signal Processors Model P522
- S5XBE Series
- Flare Stack Monitoring System Watchdog III
- Industrial Flame Monitoring Accessories
- FlameTools PC Monitoring Software and Touchscreen Display
- Signal Processors Model 700
- Signal Processors Model 600U
- U2 Series
- Signal Processors Model P531
- View All Direct Fired Furnace Burners
- ExtensoHeat
- Furnnox
- ThermJet
- KINEMAX® Medium Velocity Industrial Burner
- WIDE-RANGE® Burner
- Low NOx burner BIC..M
- Burners for gas BIC, BICA, ZIC
- Nozzle mix gas and oil burners NMC
- Triple Air Staged Ultra Low Nox Burner TriOx
- Radiant Cone Gas Burner RKG
- Burners for gas BIO, BIOA, ZIO
- Annular excess air burners
- Excess air burner BIC..L
- Beta gas and oil burners BBG/BBC
- Ceramic tube sets TSC
- WHG Wall Hugger Gas Burners WGH / Wall Hugger Gas Burners WHG-H
- Wall Hugger Invisiflame Low Nox Flat Flame Gas Burner WHI
- View All Self-Recuperative and Radiant Tube Burners
- E-Jector
- Single Ended Radiant Tube Burner (SER)
- Kromschroeder ECOMAX Self-recuperative burners
- Kromschroeder SER-C ceramic radiant tubes
- Kromschroeder SICAFLEX Segmented flame tube
- ThermJet Self-Recuperative Burner
- Tube Firing Burner
- Bayonet Ultra Recuperator
- UNI-RAD® Radiant Tube Burner
- Low NOx Self-Recuperative Burners ECOMAX LE
- Burner with integrated recuperator BICR
- View All Single Burners
- RatioAir
- RatioMatic
- InciniCone
- ThermAir
- Vortometric
- Winnox
- OVENPAK® 500 Series
- OVENPAK® LE Burner
- OPTIMA™ SLS Burner
- SLS™ Technology
- KINEDIZER® LE
- MEGAFIRE® HD Industrial Burner
- OVENPAK® 400 Series
- VALUPAK®-II
- XPO™ Indirect Burner
- M-PAKT® Ultra Low NOX
- Packaged burner system HeatPak
- View All Fixed Gauging
- Lidec Liquid Level Switch
- Communication Interface Unit
- CT801 Electropneumatic Level Transmitters
- Spare Parts & Accessories - Marine Fixed Gauging
- Water Ingress Detection System
- CargoBoss Tank Gauging Software
- T901 Temperature and Pressure Transmitters
- CARLA Overfill Detection System
- PL3700X Pressure and Level Transmitters
- EM540 & EM940 Radar Level Gauge
- View All Oil Accessories
- Maxon LO Light Oil Supply Units
- Oil Viscosity Control OVC
- Flexible Metal Oil Hose FOH
- Oil Pump & Motor Sets RP
- Oil Filters OF
- Oil-Air Ratio Regulators MRO
- Oil Line
- Temperature Indicators TI
- Oil Flow Meters FMO
- Oil Pressure Relief Valves OPRV
- Electric Oil Line Heater LHE
- Line Heater Oil LHO
- Hauck Oil Supply Pumping Unit SPU
- Oil Pressure Regulators PRO
- Electric Suction Oil Heaters SHE
- Oil Pressure Regulators OPR
- View All Honeywell Forge Advanced Process Control
- Honeywell Forge Advanced Process Control | Plant-Wide Otimizer
- Honeywell Forge Advanced Process Control | Control Performance Analytics
- Honeywell Forge Advanced Process Control | Multivariable Controller
- Honeywell Forge Advanced Process Control|Control Performance Monitor
- Honeywell Forge Advanced Process Control|Taiji PID
- Honeywell Forge Advanced Process Control|Multi-Unit Optimizer
- Honeywell Forge Advanced Process Control | Online Modeler
- Honeywell Forge Advanced Process Control | Soft Sensors
- View All Honeywell Forge Blending & Movement Management
- Honeywell Forge Blending & Movement Management |BLEND
- Honeywell Forge Blending & Movement Management |Experion Blend Controller
- Honeywell Forge Blending & Movement Management |LIMS Viewer
- Honeywell Forge Blending & Movement Management |Profit Movement Management - Movement Monitor
- Honeywell Forge Blending & Movement Management | Profit Movement Management - Movement Control
- Honeywell Forge Blending & Movement Management | Profit Inventory Monitor
- Honeywell Forge Blending & Movement Management | Blending Instructions
- Honeywell Forge Blending & Movement Management | Profit Blend Controller
- Honeywell Forge Blending & Movement Management| Experion Tank Monitor
- Honeywell Forge Blending & Movement Management | Profit Blend Optimizer
- Honeywell Forge Blending & Movement Management | Profit Blend Performance Monitor
- View All Honeywell Forge Corrosion Advisor
- Honeywell Forge Corrosion Advisor |Predict®-RT
- Honeywell Forge Corrosion Advisor |Predict®-Crude
- Honeywell Forge Corrosion Advisor |Predict®-Pipe
- Honeywell Forge Corrosion Advisor |Predict®-Amine
- Honeywell Forge Corrosion Advisor |Predict®
- Honeywell Forge Corrosion Advisor |Strategy-A
- Honeywell Forge Corrosion Advisor |Socrates
- Honeywell Forge Corrosion Advisor |Risk IT
- Honeywell Forge Corrosion Advisor |Predict®-SW
- Honeywell Forge Corrosion Advisor |Predict®-SA
- View All Honeywell Forge Process Simulation
- UniSim® Design|UniSim Design Suite
- UniSim® Design|UniSim EO (Equation Oriented)
- UniSim® Design|UniSim Optimize
- UniSim® Design|UniSim Case Linker
- UniSim® Design|UniSim Dynamic Option
- UniSim® Design|UniSim Thermo WorkBench
- UniSim® Design|UniSim Spiral Wound Tube Bundle
- UniSim® Design|UniSim Gasifier
- UniSim® Design|UniSim Flare
- UniSim® Design|UniSim Refining Reactors
- UniSim® Design|UniSim PRS
- UniSim® Design|UniSim Blowdown Customize
- UniSim® Design|UniSim ExchangerNet Operations Option
- UniSim® Design|UniSim ExchangerNet
- UniSim® Design|UniSim Heat Exchangers
-
Services
Services
-
Combustion Safety
Honeywell Combustion Safety (HCS) is the industry leader in the field of combustion safety; providing expert consulting, training and engineering services for all types of fuel-fired equipment. As the largest independent fuel train safety testing company in the world, we offer a comprehensive inspection program. Each year, HCS inspects thousands of fuel trains and fuel-fired equipment globally across industries such as Automotive, Food & Beverage, Building Materials and Pharmaceutical.
-
Cyber Security Services
Engage with our OT (Operational Technology) cybersecurity experts for onsite consulting services, or extend your cybersecurity operations to remotely monitor and manage your cybersecurity and detect threats early through Managed Security Services offering. Our service offerings helps you to rapidly engage cybersecurity expertise, knowledge and training wihtout the need for in-house hiring, allowing companies to focus their valuable resources to drive business results while avoding production loss.
- Fire & Gas Services
-
Control System Services
Whether you’re looking to address a skilled labor shortage, modernize systems, optimize performance, mitigate safety or cybersecurity risks, or take full advantage of remote connectivity. HONEYWELL WILL HELP YOU PROTECT AND SHAPE YOUR FUTURE
-
Training
Skills shortages, remote working and digital technologies are changing the way we work. Honeywell Academy is the single-stop for solutions to accelerate and enhance competencies for all your workers
-
Combustion Safety
-
Solutions
Solutions
- Batch Automation
- Workforce Excellence
-
Honeywell Forge
- Workforce-Productivity
- Smarter-Asset-Performance-Management
- Workforce-productivity-forge-worker-assist
- Workforce-Competency
- Advanced Process Control
- Honeywell Forge Workforce Competency
- Profit-Performance-Monitor
- Honeywell Forge Workforce Productivity
- Honeywell forge worker assist
- forge-inspection-rounds
- Honeywell Forge for Industrial
-
Support
Support
You are browsing the product catalog for
Reduce Scrap rates and enhance efficiency
Lithium Ion Battery Manufacturing
Honeywell is recognized globally by Lithium Ion Battery manufacturers as a knowledgeable measurement partner that understands their unique industry requirements and offers expert insights to help elevate their business performance.
Honeywell’s advanced measurement and control technology is used in many critical areas of Lithium Ion Battery manufacturing, from the initial mixing process for anode and cathode electrodes to material coating, drying, winding/unwinding, calendering, etc.
Honeywell helps customers with Greenfield operations who are faced with reducing scrap rates when processing expensive cobalt, nickel, copper and manganese raw materials, but lack in-house automation expertise to address this problem and increase ROI.
Honeywell helps customers with existing operations upgrade to synchronized “same spot” scanning to improve the precision of foil coating and edge detection as part of their challenging production process.
Honeywell Solutions for Lithium Ion Battery Manufacturing For Greater Productivity, Improved Quality And Lower Costs.
Key benefits for customers
More than 20 years
of proven experience
Unparalleled visibility to
the product quality
Accurate measurements for automatic controls
Roll-to-Roll interface to relate real time batch data to cell-level data
A CONNECTED, INTEGRATED APPROACH FOR LITHIUM ION BATTERY MANUFACTURING
Holistic, end-to-end measurement and control capability eliminates islands of automation and helps improve production performance.
Optical Caliper Sensor
for direct thickness measurement at electrode calender/press
MXProLine
Proven platform which can integrate specialty measurement and control strategies which have been refined with decades of experience.
Superclean 5080 Scanners
Provides the basis for accurate, online measurements of basis weight and thickness of various components from conductive foils, electrodes and separators.
Basis weight Sensors
like beta, x-ray, IR to meet the diverse weight measurement needs within the LIB processes
Quality Optimizer and As-Cut-Roll
Designed for roll-base data historians with traceability down to the cell-level rolls.
QCS 4.0
Transforms data into actionable, real-time insights for improved process quality and production performance.
THE HONEYWELL DIFFERENCE
The Industrial Expertise and Knowledge That Your Business Needs
HONEYWELL FORGE
Honeywell Forge for Industrial provides actionable recommendations, highlighted with potential economic impact for intelligent business and operations.
Honeywell LEAP™
Optimizes automation project execution with capabilities such as automated device commissioning, which enables late binding of devices with loop configuration created in the cloud.
Fire & Gas Solutions
Provides measures for fire detection, aspiration, suppression and mass notification, improving situational awareness and ensuring the earliest possible notification of potential incidents.
Assurance 360 Outcome-based Services
Provides agreed service levels and takes a strategic view to minimize asset ownership costs, guarantee performance and improve business results.
Cyber Solutions
Honeywell Forge for Cybersecurity provides industrial cybersecurity software and services that help protect the world’s most critical infrastructures and strengthens measures across IIoT technologies.
Global Technical Assistance Center
Ensuring Safe, Efficient and Reliable Operations
Global Presence Local Support
What our customers say about us?
Honeywell as the base supplier for automation systems at Sappi Gratkorn has offered us a customer-oriented solution that reuses installed equipment combined with the newest DCS and QCS functions and technology.”
– Karl Weiss, Sappi Gratkorn
We selected Honeywell for reliability and trust. Their systems installed and commissioned to plan and enables us to make the quality of film we need for our customers”.
- Apostolos Kerkemezos, Marflex
With increased production and expansion into new markets, we wanted to improve our monitoring and control of our film and sheet. The MXProLine system not only allows us to look very closely at our process but we are able to achieve significant improvements in quality beyond our expectation.”
- Jonathan Heaton, Bond-A-Band, United Kingdom
CONTACT US
Copyright © 2024 Honeywell International Inc.
Maximum File Size
Maximum Files Exceeded
Due to inactivity you will be logged out in 000 seconds.
Maximum File Size
Maximum Files Exceeded
Honeywell International Inc. is committed to ensuring compliance with global laws that regulate its export and import activities. In following company procedures, it has been determined that is identified on a denied/restricted parties list that is applicable to this transaction.
As a result, Honeywell is unable to continue with this request.
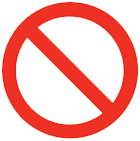