-
Currency:Localize your Content
You can set your preferred currency for this account.
Choose a Currency
Currency- CHOOSE YOUR CURRENCY
Update Currency
Changing Currency will cause your current cart to be deleted. Click OK to proceed.
To Keep your current cart, click CLOSE and then save your cart before changing currency.
-
Select Account1
Switching accounts will update the product catalog available to you. When switching accounts, your current cart will not move to the new account you select. Your current cart will be available if you log back into this account again.
Account# Account Name City Zip/Post Code My Account -
-
Products
- Complete Combustion Solutions
- Fuel & Air Delivery
- Burner Management Systems
- Burners & Heat Exchangers
- Complete Combustion Systems
- Software
- Control & Supervisory Systems
- Field Instruments
- Gas
- Marine
- Process Instruments
- Training
- Spare Parts
- Terminals
- Thermal Solutions
- Wireless
- Uncategorized
- Quality Control Systems
- Trainings
- Utilities
- View All Manual Valves & Filters
- Adjustable Orifice Valves (ALO/ALO-R)
- Manual Shutoff Valves
- Disk Type Check Valves
- A Style Synchro Valves
- Flow adjusting cocks GEHV, GEH, LEH
- Manual valves AKT
- Manual valves with thermal equipment trip AKT..TAS
- Shut off valves ZIVA
- Thermal equipment trips TAS
- Gas filters GFK
- View All Pressure Regulators
- Kromschroeder VAD-VAG-VAH-VAV pressure regulators with solenoid valve
- Safety shut-off valves JSAV
- Pressure regulators for gas GDJ
- Gas Pressure Regulators Maxon
- Pressure regulators for gas VGBF
- Pressure regulators for gas J78R, 60DJ
- Air/gas ratio controls GIK
- Relief valve VSBV
- Circulation pressure control and relief regulators VAR
- Variable air/gas ratio controls GIKH
- SmartLine Wireless Differential Pressure
- View All Shutoff Valves
- Kromschroeder VAS-VCS solenoid valves for gas
- Kromschroeder VAN magnetic relief valves
- High Pressure Electro-Mechanical Oil Shut-off Valves
- Series 8000 Air Actuated Valves for Liquid Service
- NI Series Hazardous Duty Valves
- Series 8000 Pneumatic Safety Shut-off Valves
- High Pressure Electro-Mechanical Gas Shut-off Valves
- Solenoid-operated butterfly valves for air MB 7/BVHM
- Solenoid valves for air VR
- Solenoid valves for gas VG
- Motorized valves for gas VK
- Solenoid valves for gas VGP
- View All Control Valves
- Discontinued - Honeywell SV2 combination valve
- SMARTLINK® CV Electronic Valves
- Micro Ratio Valves (M-P-O Style)
- SMARTLINK® MRV Electronic Ratio Valves
- Self-Cleaning Micro Oil Valves MOV
- Control valves RV, control valves with solenoid valve RVS
- B, F, G, & K Micro Cam Oil Valves MCOV
- Solenoid valves for gas VE, V4295
- VR400/VR800 Series
- VQ400/800 Series
- View All Pressure Switches & Gauges
- Honeywell C6097 pressure switches for gas
- Kromschroeder DL..A pressure switches for air
- Kromschroeder DG pressure switches for gas
- Kromschroeder DL..K pressure switches for air
- Kromschroeder DG..C pressure switches for gas
- Kromschroeder DL..E pressure switches for air
- Elektronic pressure gauge DMG
- Pressuretrol® Limit controllers L4079A, B, W
- Pressure gauges KFM, RFM
- Pressure Indicators PI
- PressureTrol® Pressure monitoring on/off controllers L404F, T, V
- PressureTrol® Pressure monitoring modulating controllers L91A, B
- CPS
- Pressure switches for gas DGM, DWR
- Vaporstat ® Controllers L408J
- View All Burner Control Units
- Kromschroeder BCU 400 burner control unit
- Honeywell 7800 SERIES burner control unit
- Kromschroeder IFD 258 burner control unit
- Kromschroeder IFD 244 burner control unit
- Automatic burner control units for continuous operation PFD 778
- Automatic burner control units for continuous operation IFD 450, 454
- Automatic burner control units IFS 110IM, 111IM
- Burner control unit BCU 370
- Relay module 7800 Series
- Burner control units BCU 560, BCU 565, BCU 580
- Automatic burner control units PFS 778, 748
- Burner control unit BCU 570
- Automatic burner control units PFU
- Automatic burner control units IFS 132B, 135B, 137B
- View All Flame Detectors
- Heat Block Seal
- Ignition Transformers Q652
- UV sensor for continuous operation UVC, UVD
- Flame detectors PFF
- Flame detector for continuous operation IFW 50
- UV sensors UVS
- Ultraviolet Flame Detector C7012A,C
- Flame detector IFW 15
- Ultraviolet Flame Detector C7027, C7035
- Ultraviolet Flame Detector C7927
- Ultraviolet Flame Detector C7915
- Ultraviolet Flame Detector C7076A,D
- Ultraviolet Flame Detector C7961E,F
- Ultraviolet Flame Detector C7061A,F
- View All Industrial Flame Monitoring (IFM)
- Gas Igniters GHE
- Viewing Heads S70X/S80X
- Model P532
- FASA Glass and Quartz Fiber Optics
- Signal Processors Model P522
- S5XBE Series
- Flare Stack Monitoring System Watchdog III
- Industrial Flame Monitoring Accessories
- FlameTools PC Monitoring Software and Touchscreen Display
- Signal Processors Model 700
- Signal Processors Model 600U
- U2 Series
- Signal Processors Model P531
- View All Direct Fired Furnace Burners
- ExtensoHeat
- Furnnox
- ThermJet
- KINEMAX® Medium Velocity Industrial Burner
- WIDE-RANGE® Burner
- Low NOx burner BIC..M
- Burners for gas BIC, BICA, ZIC
- Nozzle mix gas and oil burners NMC
- Triple Air Staged Ultra Low Nox Burner TriOx
- Radiant Cone Gas Burner RKG
- Burners for gas BIO, BIOA, ZIO
- Annular excess air burners
- Excess air burner BIC..L
- Beta gas and oil burners BBG/BBC
- Ceramic tube sets TSC
- WHG Wall Hugger Gas Burners WGH / Wall Hugger Gas Burners WHG-H
- Wall Hugger Invisiflame Low Nox Flat Flame Gas Burner WHI
- View All Self-Recuperative and Radiant Tube Burners
- E-Jector
- Single Ended Radiant Tube Burner (SER)
- Kromschroeder ECOMAX Self-recuperative burners
- Kromschroeder SER-C ceramic radiant tubes
- Kromschroeder SICAFLEX Segmented flame tube
- ThermJet Self-Recuperative Burner
- Tube Firing Burner
- Bayonet Ultra Recuperator
- UNI-RAD® Radiant Tube Burner
- Low NOx Self-Recuperative Burners ECOMAX LE
- Burner with integrated recuperator BICR
- View All Single Burners
- RatioAir
- RatioMatic
- InciniCone
- ThermAir
- Vortometric
- Winnox
- OVENPAK® 500 Series
- OVENPAK® LE Burner
- OPTIMA™ SLS Burner
- SLS™ Technology
- KINEDIZER® LE
- MEGAFIRE® HD Industrial Burner
- OVENPAK® 400 Series
- VALUPAK®-II
- XPO™ Indirect Burner
- M-PAKT® Ultra Low NOX
- Packaged burner system HeatPak
- View All Fixed Gauging
- Lidec Liquid Level Switch
- Communication Interface Unit
- CT801 Electropneumatic Level Transmitters
- Spare Parts & Accessories - Marine Fixed Gauging
- Water Ingress Detection System
- CargoBoss Tank Gauging Software
- T901 Temperature and Pressure Transmitters
- CARLA Overfill Detection System
- PL3700X Pressure and Level Transmitters
- EM540 & EM940 Radar Level Gauge
- View All Oil Accessories
- Maxon LO Light Oil Supply Units
- Oil Viscosity Control OVC
- Flexible Metal Oil Hose FOH
- Oil Pump & Motor Sets RP
- Oil Filters OF
- Oil-Air Ratio Regulators MRO
- Oil Line
- Temperature Indicators TI
- Oil Flow Meters FMO
- Oil Pressure Relief Valves OPRV
- Electric Oil Line Heater LHE
- Line Heater Oil LHO
- Hauck Oil Supply Pumping Unit SPU
- Oil Pressure Regulators PRO
- Electric Suction Oil Heaters SHE
- Oil Pressure Regulators OPR
- View All Honeywell Forge Advanced Process Control
- Honeywell Forge Advanced Process Control | Plant-Wide Otimizer
- Honeywell Forge Advanced Process Control | Control Performance Analytics
- Honeywell Forge Advanced Process Control | Multivariable Controller
- Honeywell Forge Advanced Process Control|Control Performance Monitor
- Honeywell Forge Advanced Process Control|Taiji PID
- Honeywell Forge Advanced Process Control|Multi-Unit Optimizer
- Honeywell Forge Advanced Process Control | Online Modeler
- Honeywell Forge Advanced Process Control | Soft Sensors
- View All Honeywell Forge Blending & Movement Management
- Honeywell Forge Blending & Movement Management |BLEND
- Honeywell Forge Blending & Movement Management |Experion Blend Controller
- Honeywell Forge Blending & Movement Management |LIMS Viewer
- Honeywell Forge Blending & Movement Management |Profit Movement Management - Movement Monitor
- Honeywell Forge Blending & Movement Management | Profit Movement Management - Movement Control
- Honeywell Forge Blending & Movement Management | Profit Inventory Monitor
- Honeywell Forge Blending & Movement Management | Blending Instructions
- Honeywell Forge Blending & Movement Management | Profit Blend Controller
- Honeywell Forge Blending & Movement Management| Experion Tank Monitor
- Honeywell Forge Blending & Movement Management | Profit Blend Optimizer
- Honeywell Forge Blending & Movement Management | Profit Blend Performance Monitor
- View All Honeywell Forge Corrosion Advisor
- Honeywell Forge Corrosion Advisor |Predict®-RT
- Honeywell Forge Corrosion Advisor |Predict®-Crude
- Honeywell Forge Corrosion Advisor |Predict®-Pipe
- Honeywell Forge Corrosion Advisor |Predict®-Amine
- Honeywell Forge Corrosion Advisor |Predict®
- Honeywell Forge Corrosion Advisor |Strategy-A
- Honeywell Forge Corrosion Advisor |Socrates
- Honeywell Forge Corrosion Advisor |Risk IT
- Honeywell Forge Corrosion Advisor |Predict®-SW
- Honeywell Forge Corrosion Advisor |Predict®-SA
- View All Honeywell Forge Process Simulation
- UniSim® Design|UniSim Design Suite
- UniSim® Design|UniSim EO (Equation Oriented)
- UniSim® Design|UniSim Optimize
- UniSim® Design|UniSim Case Linker
- UniSim® Design|UniSim Dynamic Option
- UniSim® Design|UniSim Thermo WorkBench
- UniSim® Design|UniSim Spiral Wound Tube Bundle
- UniSim® Design|UniSim Gasifier
- UniSim® Design|UniSim Flare
- UniSim® Design|UniSim Refining Reactors
- UniSim® Design|UniSim PRS
- UniSim® Design|UniSim Blowdown Customize
- UniSim® Design|UniSim ExchangerNet Operations Option
- UniSim® Design|UniSim ExchangerNet
- UniSim® Design|UniSim Heat Exchangers
-
Services
Services
-
Combustion Safety
Honeywell Combustion Safety (HCS) is the industry leader in the field of combustion safety; providing expert consulting, training and engineering services for all types of fuel-fired equipment. As the largest independent fuel train safety testing company in the world, we offer a comprehensive inspection program. Each year, HCS inspects thousands of fuel trains and fuel-fired equipment globally across industries such as Automotive, Food & Beverage, Building Materials and Pharmaceutical.
-
Cyber Security Services
Engage with our OT (Operational Technology) cybersecurity experts for onsite consulting services, or extend your cybersecurity operations to remotely monitor and manage your cybersecurity and detect threats early through Managed Security Services offering. Our service offerings helps you to rapidly engage cybersecurity expertise, knowledge and training wihtout the need for in-house hiring, allowing companies to focus their valuable resources to drive business results while avoding production loss.
- Fire & Gas Services
-
Control System Services
Whether you’re looking to address a skilled labor shortage, modernize systems, optimize performance, mitigate safety or cybersecurity risks, or take full advantage of remote connectivity. HONEYWELL WILL HELP YOU PROTECT AND SHAPE YOUR FUTURE
-
Training
Skills shortages, remote working and digital technologies are changing the way we work. Honeywell Academy is the single-stop for solutions to accelerate and enhance competencies for all your workers
-
Combustion Safety
-
Solutions
Solutions
- Batch Automation
- Workforce Excellence
-
Honeywell Forge
- Workforce-Productivity
- Smarter-Asset-Performance-Management
- Workforce-productivity-forge-worker-assist
- Workforce-Competency
- Advanced Process Control
- Honeywell Forge Workforce Competency
- Profit-Performance-Monitor
- Honeywell Forge Workforce Productivity
- Honeywell forge worker assist
- forge-inspection-rounds
- Honeywell Forge for Industrial
-
Support
Support
You are browsing the product catalog for
Honeywell Forge for Industrial
Find the Quickest Path to Sustain Peak Performance
HONEYWELL FORGE FOR INDUSTRIAL
Enterprise Performance Management
Honeywell Forge for Industrial provides actionable recommendations, highlighted with potential economic impact for intelligent business and operations. The portable and extensible software solution uses process and asset digital twins, role based, and comprehensive analytics to enable top to bottom enterprise-wide visibility improving decision making and sustaining overall performance of the process, assets, people and safety.
- $7M annually from optimization recommendations
- $3M annually through energy savings
- $1.2M annually from process efficiencies
SUSTAINED PEAK PERFORMANCE
WHAT IS IT?
An Enterprise Performance Management software solution that goes beyond data consultation and visualization. Through the integration of process and asset digital twins, and building on domain expertise, Honeywell Forge provides deep enterprise-wide insights and intelligent recommendations for sustained peak performance.
IT ADDRESSES MARKET CHALLENGES
- Connects and integrates siloed data systems
- Enables companies to do more with less and run assets longer in harsher operating conditions
- Overcomes the loss of subject matter expertise and differing shift outcomes due to increased velocity through positions
IT BUILDS ON EXISTING SYSTEMS
- No need to rip-out systems, just build on top of existing platforms
- Connects Honeywell, Customer and Partner expertise for enterprise-wide insights
- Portable and supports multi-mode deployment in the cloud or on-premises
IT IS BUILT ON DOMAIN EXPERTISE
- Builds on knowledge from 100 years of Honeywell’s domain expertise
- captures and continuously improves knowledge across the enterprise
- Built to the latest cyber security standards, with IP Protection
HONEYWELL FORGE
Honeywell Forge Process Reliability Advisor
Honeywell Forge Process Optimization Advisor
Honeywell Forge Profit Performance Monitor
Honeywell Forge Asset Performance Management
CASE STUDIES
LEARN MORE
Contact Us
Copyright © 2024 Honeywell International Inc.
Maximum File Size
Maximum Files Exceeded
Due to inactivity you will be logged out in 000 seconds.
Maximum File Size
Maximum Files Exceeded
Honeywell International Inc. is committed to ensuring compliance with global laws that regulate its export and import activities. In following company procedures, it has been determined that is identified on a denied/restricted parties list that is applicable to this transaction.
As a result, Honeywell is unable to continue with this request.
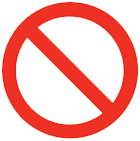